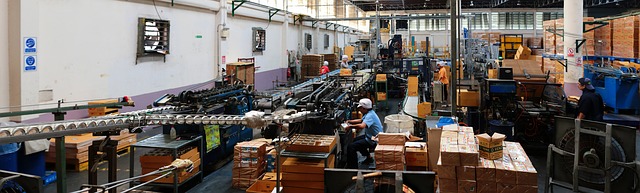
Industrial processes offer a very important source of energy efficiency, all the more important to exploit as these processes are evolving and that a permanent attention is required to maintain a performance of good level.
Energy service providers praising their know-how in the industry are quite rare. Tertiary buildings make more money. But, by looking closely, most of them have a “peripheral” approach of industrial processes: they propose the installation of a generation on site, not very related to the process, as well as actions of energy efficiency on the utilities of the process (compressed air, lighting, heating).
Only a few companies, mainly start-ups, propose to target the processes themselves, through energy efficiency actions, or via a data analysis platform.
Why this situation?
Addressing the energy efficiency of industrial processes involves three conditions:
1- Have access to relevant data
The first reflex is to work from the available data, those acquired by automata and controllers of all kinds. This first approach emphasizes the ability to acquire these data, ie on communication protocol issues.
But this data may be insufficient: the data acquisition point defines the angle at which a process can be observed. A bit like facing a complex object, a new angle of view can give access to a better understanding of energy consumption. This second stage of analysis involves the installation of new sensors: this can be too expensive unless you use solutions like Centrica / Panoramic Power or Gulplug / Save it yourself. These sensors respond, in addition, to the need to adjust the location of the measurement for optimal vision of the energy flows.
2- To be perceived as a credible actor by the industrial client
An industrialist has two fears about an external stakeholder: access to confidential information and the preservation of its productivity.
The first fear often pushes him to integrate skills rather than calling on an outsider. In this case, any energy support can only be indirect. At least initially.
Because of his second fear, an industrial client requires an interlocutor understanding or knowing his trade. This condition guarantees in his eyes not to waste too much time explaining the specificities and constraints of his process but especially not to take the risk of passing energy savings before productivity. This requirement is all the more important with manufacturing managers, who are often in charge of setting up energy efficiency actions.
3- Have energy skills
This condition may seem trivial but the energy knowledge of engines, furnaces, conveyors and other special machines is of course essential as well as the ability to understand the systemic dimension of a process: energy optimization of the use of each machine or part of a process does not automatically mean global energy optimization.
These three conditions are not simple to bring together. At the same time, the necessary skills and the work process are very specific and demanding and transform the energy efficiency of industrial processes into a minefield where the first misstep can jeopardize the trust of the customer.
Here is an area where competitive intensity will not be very high!
Subscribe to receive every quarter all articles of the blog: [sibwp_form id=2]
Leave a Reply